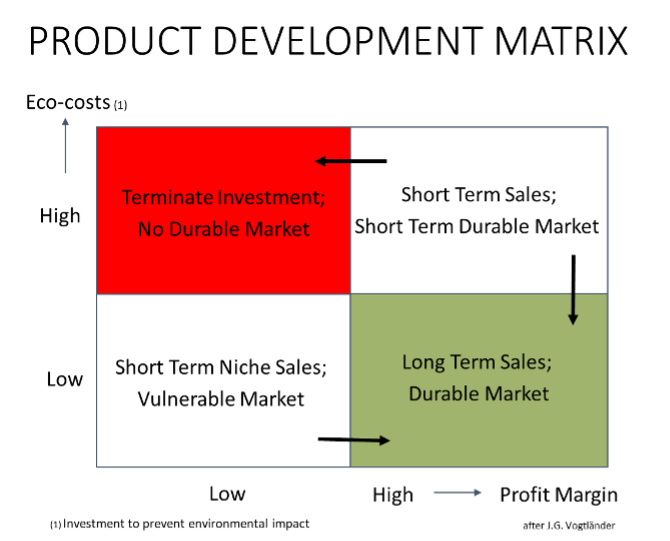
The challenges of moving to the profitable green quarter of Sustainable Endeavour’s “Product Development Matrix” can appear daunting. At first glance, the potential of falling into the unprofitable red “trap” is likely to discourage green investment in sustainability. The reality, however, is that properly channeled investment can result in eco-costs reduction, new and greater product value to customers and translate into higher sales. This is the case for Dee Zee, a staple brand in the truck accessory market since 1977.
Located in Des Moines, Iowa, USA, Dee Zee produces metal vehicle accessories such as tool boxes, running boards, truck racks, transfer tanks, and tailgate assist devices for original equipment manufacturers (OEM). Their customers have included Stellantis (formerly known as Chrysler), Ford, GM, Honda, Nissan, Subaru, and Toyota. Almost all of Dee Zee’s manufacturing takes place in the Des Moines vicinity. However, a fraction of Dee Zee’s components are imported from support locations abroad.
Dee Zee is committed to promoting sustainability and green manufacturing techniques based on lean manufacturing practices. As a matter of routine business, Dee Zee has realized opportunities to reduce its environmental and carbon footprints through recycling, material reductions, and efficient manufacturing processes. Recently, Dee Zee has identified additional opportunities to reduce packaging and transportation costs and scope three (third party) CO2 emissions and their customers are going to love the efforts!
During the transportation of Dee Zee’s products, a great deal of corrugated and foam packaging material is required to maintain the visually appealing characteristics, so important to the company’s end consumers. As a result of recent investments in packaging redesign, however, Dee Zee has reduced the quantity of corrugated and foam used in shipment by 3.3 lbs. per every 2 running boards shipped from overseas suppliers. That equals the elimination of a whopping 146 tons total shipping weight per year and the associated transportation costs! In 2021, Dee Zee also intends to replace molded foam packaging material with a recyclable corrugated insert and increase the product per pallet density from 12 to 30 boxes. Together, raising the density per shipping unit will reduce the number of international shipping containers by 27 per year.
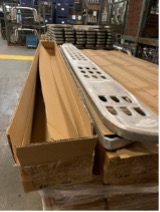
Former Packaging: Pads & Box
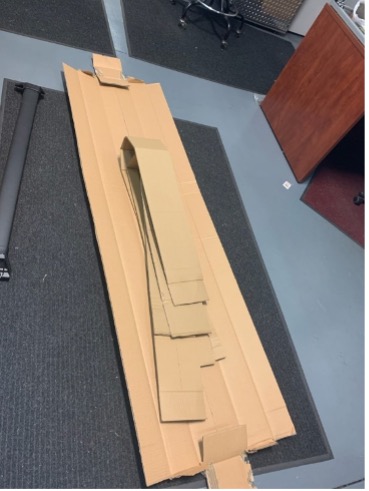
Corrugated Waste 3.3 lbs.
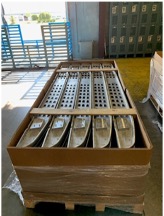
Proposed Packaging
Dee Zee’s efforts translate into both producer cost economies and increased product value for customers like Toyota. Since 2016, the OEM has obliged it’s suppliers to participate in “Green Purchasing” initiatives, three of which are particularly relevant to Dee Zee. First, Toyota has requested all Tier 1 suppliers to initiate packaging material reduction efforts in line with Toyota’s goal to reduce the use of packaging material by 1 percent per year. Toyota’s goals include increasing use of returnable and/or recycled packaging and reducing the use of disposable wood pallets, cardboard and plastic packaging. By addressing its own packaging design, Dee Zee is demonstrating a consistent willingness to support in its customer’s values and initiatives.
Second, Toyota’s “Green Purchasing” guidelines instruct suppliers to identify “…alternative transport technologies that have the potential to further reduce CO2 emissions.” Toyota’s established target is to reduce life cycle CO2 emissions to zero as part of the Environmental Challenge 2050. As a result, Toyota collects supplier data on distance traveled, fuel efficiency, and GHG efficiency. Dee Zee will be able to apply the volume of shipping CO2 reduced to Toyota’s life cycle target. In fact, between port to port (ship) and port to site (diesel truck) transportation, Dee Zee’s total appreciable CO2 reduction will equal 36,555 kg per year. Monetized[1], this equals an annual eco-cost savings of $12,230 (10,080 €). As indicated in the Product Development Matrix above, Dee Zee’s return on investment in packaging efficiency will be realized in terms of reduced future costs to prevent environmental impacts from CO2 emissions and increased appeal of Dee Zee’s product portfolio to customers like Toyota.
Finally, Toyota requires certain production suppliers to implement a functional ISO 14001 environmental management system (EMS) for third party certification. ISO 14001 provides an analytical tool that drives organizations to investigate, identify and realize hidden value such as opportunities to reduce packaging volume, valuable cargo space and the associated CO2 emissions generated during intercontinental transportation. Dee Zee has had an implemented and certified ISO 14001 EMS since 2003.
Dee Zee’s efforts to reduce packaging materials, CO2 transportation emissions and shipping costs, and maintain a certified EMS are instructive on how to employ sustainability to increase product value for customers. Where could this philosophy take your company? Could a similar journey be in store for the future?
Sustainable Endeavour, Todd Heller, Erik Wijlhuizen February, 2021
[1] DELFT UNIVERSITY OF TECHNOLOGY, “Excel files: Idemat and Ecoinvent and Ecocosts Substances,” 2021, Rev. A, https://www.ecocostsvalue.com/data/ (accessed February 10, 2021).